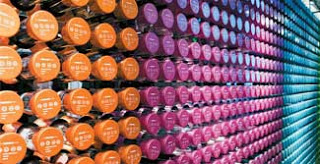
No tempo que você levará para ler esta reportagem, cerca de 50 000 sacolinhas plásticas serão consumidas no Brasil. A média nacional é de 1,5 milhão por hora. Embora representem pouco individualmente, os saquinhos de supermercado formam um volume enorme de lixo, que pode demorar vários séculos para se decompor no ambiente. Como reduzir o impacto causado pelo plástico na natureza é uma preocupação crescente. Por isso, ganham cada vez mais espaço as iniciativas de produzir plástico a partir de matérias-primas renováveis, como a cana- de-açúcar e o milho.
Universidades e empresas trabalham em projetos conjuntos para identificar novos materiais e formas de melhorar asaplicações dos plásticos de origem renovável. Existem várias linhas de pesquisa e produção, que geram produtos recicláveis e/ou biodegradáveis. Uma peça plástica que será usada por muitos anos, por exemplo, não precisa ser biodegradável, mas é importante que seja reciclável. Já uma sacola de supermercado, que provavelmente será usada para acondicionar lixo doméstico, deve ser biodegradável.
Nos laboratórios da Universidade Estadual de Londrina (UEL), no Paraná, os pesquisadores produzem plásticos a partir de amido de mandioca. Os estudos já são feitos há dez anos e nos últimos quatro eles passaram a incorporar também uma porcentagem de fibra de cana-de-açúcar. “Começamos a ver que havia dificuldades na produção porque a mistura não era adequada para o processo industrial”, diz Fábio Yamashita, professor do departamento de Ciência e Tecnologia de Alimentos da UEL. Mais recentemente, os pesquisadores decidiram misturar o amido de mandioca a um polímero fabricado pela Basf ainda com origem petroquímica, o Ecoflex. O resultado foi um produto com algumas das características de que a indústria precisa.
Com a mistura foi possível testar o uso do plástico biodegradável em atividades no campo. Os principais usos até agora foram para a cobertura de campos para a plantação de morango, o ensacamento de goiabas na fase de crescimento, para evitar o ataque de pragas, e a embalagem de mudas de plantas medicinais, em saquinhos que geralmente são retirados antes do plantio. Os testes nos campos de morango foram feitos em escala commercial e mostraram que é preciso calibrar a velocidade de degradação do fi lme plástico. “Ele começou a se deteriorar antes do tempo”, afirma Yamashita. Na Universidade Federal de São Carlos (UFSCar), no interior paulista, há estudos na mesma linha. A engenheira de materiais Marília Motomura trabalhou com amido de mandioca, fibra de coco e serragem de madeira. Ela misturou as matérias- primas ao Ecoflex para ampliar as opções de uso do plástico biodegradável, que pode fi car mais rígido ou fl exível, por exemplo. Essas características são fundamentais para determinar que tipo de produto final é possível produzir. “A aplicação ainda é restrita. Apenas as peças feitas por processo de extrusão já estão sendo vendidas”, diz Marília.
A INDÚSTRIA INVESTE PESADO
Diante da demanda global por attitudes mais verdes, as empresas precisaram se munir de alternativas para oferecer ao mercado. A Braskem, oitava maior petroquímica do mundo, abriu em setembro do ano passado sua primeira filial destinada a produzir apenas plástico verde. A fábrica, que fica em Triunfo, no Rio Grande do Sul, recebeu 500 milhões de reais de investimento e tem capacidade de produzir 200 000 toneladas anuais de plástico verde. A estratégia adotada pela Braskem é usar etanol como matéria- prima. Depois de um processo de desidratação do etanol, a empresa obtém o eteno, empregado na fabricação do polietileno. É ele que a Braskem vende a outras companhias, que podem usá-lo da mesma forma que o polietileno obtido a partir do petróleo.
Essa substituição é semelhante à troca da gasolina pelo álcool nos carros. A matéria- prima é renovável. O plástico verde permite a reciclagem, mas ele não é biodegradável.
“O balanço ambiental da produção com etanol é mais favorável. Para cada tonelada de plástico verde é possível sequestrar 2,5 toneladas de gás carbônico da atmosfera”, afirma Antônio Queiroz, diretor de tecnologia da Braskem.
Diversas empresas nacionais estão usando embalagens feitas com o plástico verde. Ele está nos refis do sabonete cremoso Erva Doce, da Natura; na linha Sundown, da Johnson & Johnson; e nas peças do jogo Banco Imobiliário, da Estrela.
A Basf também está investindo no plástico ecológico. Desde 2000, a empresa produz o polímero Ecoflex (usado nas pesquisas da UEL e da UFSCar), que está disponível no Brasil desde 2007. Sua estrutura permite o ataque dos microorganismos no processo de compostagem, o que o torna biodegradável. A partir dele surgiram variações, como o Ecobras e o Ecovio. O primeiro foi desenvolvido em parceria com universidades e com a empresa Corn Products e usa amido de milho na mistura. O segundo leva ácido poliláctico, derivado do ácido láctico. O Ecoflex é empregado pela Honda para revestir os bancos dos modelos Fit e New Civic. Já o Ecovio está em sacolinhas de supermercado.
Quem também usa o ácido poliláctico é a Cargill, que fabrica nos *Estados Unidos o biopolímero Ingeo, que é similar ao PET das garrafas plásticas e pode substituí-lo em
diversas aplicações.
“O bioplástico tem o maior número de opções de descarte pós consumo. Ele pode ser reciclado mecânica ou quimicamente e é biodegradável em condições de compostagem”, diz Walcinyr Bragatto Neto, gerente de produto da Cargill.
O plástico foi empregado na loja con ceito da Track&Field, que vende roupas esportivas,em Nova York. Todas as peças da loja ficam expostas em tubos plásticos presos às paredes. Além de facilitar o estoque e a exposição das peças, as belas embalagens são reutilizáveis.
SUBSTITUIÇÃO A CONTA-GOTAS
Por mais que surjam opções viáveis de plástico feito com matéria-prima renovável, a troca total a longo prazo ainda é vista como improvável
“É uma utopia querer substituir tudo”, diz Letícia Mendonça, gerente do negócio de especialidades plásticas da Basf para a América do Sul.
O futuro dos plásticos verdes depende da escala que eles atingirem. Sem volume de produção o preço não cai, o que inviabiliza a ampla adoção. Hoje, o plástico ecológico custa pelo menos 20% a mais que o de origem fóssil. A estimativa é que chegue a apenas 20% do total de plásticos produzidos no mundo até 2030. Enquanto a abrangência não aumenta, uma saída é não usar plástico quando há outras opções. Nos últimos 18 meses, 5 bilhões de sacolinhas plásticas foram substituídas por ecobags ou caixas de papelão. Já é um número e tanto.
*Enquanto no Brasil a cana-de-açúcar é usada na produção de plástico verde, nos Estados Unidos a principal materia prima é o milho. Aqui a estimativa de produção para 2010 foi de 52,5 milhões de toneladas. A produção industrial recebe uma parcela pequena (9%) e a maior fatia vai para a criação de animais (75%). Renata Leal
Info Exame – 03/2011
Fonte: Planeta Sustentável
Universidades e empresas trabalham em projetos conjuntos para identificar novos materiais e formas de melhorar asaplicações dos plásticos de origem renovável. Existem várias linhas de pesquisa e produção, que geram produtos recicláveis e/ou biodegradáveis. Uma peça plástica que será usada por muitos anos, por exemplo, não precisa ser biodegradável, mas é importante que seja reciclável. Já uma sacola de supermercado, que provavelmente será usada para acondicionar lixo doméstico, deve ser biodegradável.
Nos laboratórios da Universidade Estadual de Londrina (UEL), no Paraná, os pesquisadores produzem plásticos a partir de amido de mandioca. Os estudos já são feitos há dez anos e nos últimos quatro eles passaram a incorporar também uma porcentagem de fibra de cana-de-açúcar. “Começamos a ver que havia dificuldades na produção porque a mistura não era adequada para o processo industrial”, diz Fábio Yamashita, professor do departamento de Ciência e Tecnologia de Alimentos da UEL. Mais recentemente, os pesquisadores decidiram misturar o amido de mandioca a um polímero fabricado pela Basf ainda com origem petroquímica, o Ecoflex. O resultado foi um produto com algumas das características de que a indústria precisa.
Com a mistura foi possível testar o uso do plástico biodegradável em atividades no campo. Os principais usos até agora foram para a cobertura de campos para a plantação de morango, o ensacamento de goiabas na fase de crescimento, para evitar o ataque de pragas, e a embalagem de mudas de plantas medicinais, em saquinhos que geralmente são retirados antes do plantio. Os testes nos campos de morango foram feitos em escala commercial e mostraram que é preciso calibrar a velocidade de degradação do fi lme plástico. “Ele começou a se deteriorar antes do tempo”, afirma Yamashita. Na Universidade Federal de São Carlos (UFSCar), no interior paulista, há estudos na mesma linha. A engenheira de materiais Marília Motomura trabalhou com amido de mandioca, fibra de coco e serragem de madeira. Ela misturou as matérias- primas ao Ecoflex para ampliar as opções de uso do plástico biodegradável, que pode fi car mais rígido ou fl exível, por exemplo. Essas características são fundamentais para determinar que tipo de produto final é possível produzir. “A aplicação ainda é restrita. Apenas as peças feitas por processo de extrusão já estão sendo vendidas”, diz Marília.
A INDÚSTRIA INVESTE PESADO
Diante da demanda global por attitudes mais verdes, as empresas precisaram se munir de alternativas para oferecer ao mercado. A Braskem, oitava maior petroquímica do mundo, abriu em setembro do ano passado sua primeira filial destinada a produzir apenas plástico verde. A fábrica, que fica em Triunfo, no Rio Grande do Sul, recebeu 500 milhões de reais de investimento e tem capacidade de produzir 200 000 toneladas anuais de plástico verde. A estratégia adotada pela Braskem é usar etanol como matéria- prima. Depois de um processo de desidratação do etanol, a empresa obtém o eteno, empregado na fabricação do polietileno. É ele que a Braskem vende a outras companhias, que podem usá-lo da mesma forma que o polietileno obtido a partir do petróleo.
Essa substituição é semelhante à troca da gasolina pelo álcool nos carros. A matéria- prima é renovável. O plástico verde permite a reciclagem, mas ele não é biodegradável.
“O balanço ambiental da produção com etanol é mais favorável. Para cada tonelada de plástico verde é possível sequestrar 2,5 toneladas de gás carbônico da atmosfera”, afirma Antônio Queiroz, diretor de tecnologia da Braskem.
Diversas empresas nacionais estão usando embalagens feitas com o plástico verde. Ele está nos refis do sabonete cremoso Erva Doce, da Natura; na linha Sundown, da Johnson & Johnson; e nas peças do jogo Banco Imobiliário, da Estrela.
A Basf também está investindo no plástico ecológico. Desde 2000, a empresa produz o polímero Ecoflex (usado nas pesquisas da UEL e da UFSCar), que está disponível no Brasil desde 2007. Sua estrutura permite o ataque dos microorganismos no processo de compostagem, o que o torna biodegradável. A partir dele surgiram variações, como o Ecobras e o Ecovio. O primeiro foi desenvolvido em parceria com universidades e com a empresa Corn Products e usa amido de milho na mistura. O segundo leva ácido poliláctico, derivado do ácido láctico. O Ecoflex é empregado pela Honda para revestir os bancos dos modelos Fit e New Civic. Já o Ecovio está em sacolinhas de supermercado.
Quem também usa o ácido poliláctico é a Cargill, que fabrica nos *Estados Unidos o biopolímero Ingeo, que é similar ao PET das garrafas plásticas e pode substituí-lo em
diversas aplicações.
“O bioplástico tem o maior número de opções de descarte pós consumo. Ele pode ser reciclado mecânica ou quimicamente e é biodegradável em condições de compostagem”, diz Walcinyr Bragatto Neto, gerente de produto da Cargill.
O plástico foi empregado na loja con ceito da Track&Field, que vende roupas esportivas,em Nova York. Todas as peças da loja ficam expostas em tubos plásticos presos às paredes. Além de facilitar o estoque e a exposição das peças, as belas embalagens são reutilizáveis.
SUBSTITUIÇÃO A CONTA-GOTAS
Por mais que surjam opções viáveis de plástico feito com matéria-prima renovável, a troca total a longo prazo ainda é vista como improvável
“É uma utopia querer substituir tudo”, diz Letícia Mendonça, gerente do negócio de especialidades plásticas da Basf para a América do Sul.
O futuro dos plásticos verdes depende da escala que eles atingirem. Sem volume de produção o preço não cai, o que inviabiliza a ampla adoção. Hoje, o plástico ecológico custa pelo menos 20% a mais que o de origem fóssil. A estimativa é que chegue a apenas 20% do total de plásticos produzidos no mundo até 2030. Enquanto a abrangência não aumenta, uma saída é não usar plástico quando há outras opções. Nos últimos 18 meses, 5 bilhões de sacolinhas plásticas foram substituídas por ecobags ou caixas de papelão. Já é um número e tanto.
*Enquanto no Brasil a cana-de-açúcar é usada na produção de plástico verde, nos Estados Unidos a principal materia prima é o milho. Aqui a estimativa de produção para 2010 foi de 52,5 milhões de toneladas. A produção industrial recebe uma parcela pequena (9%) e a maior fatia vai para a criação de animais (75%). Renata Leal
Info Exame – 03/2011
Fonte: Planeta Sustentável